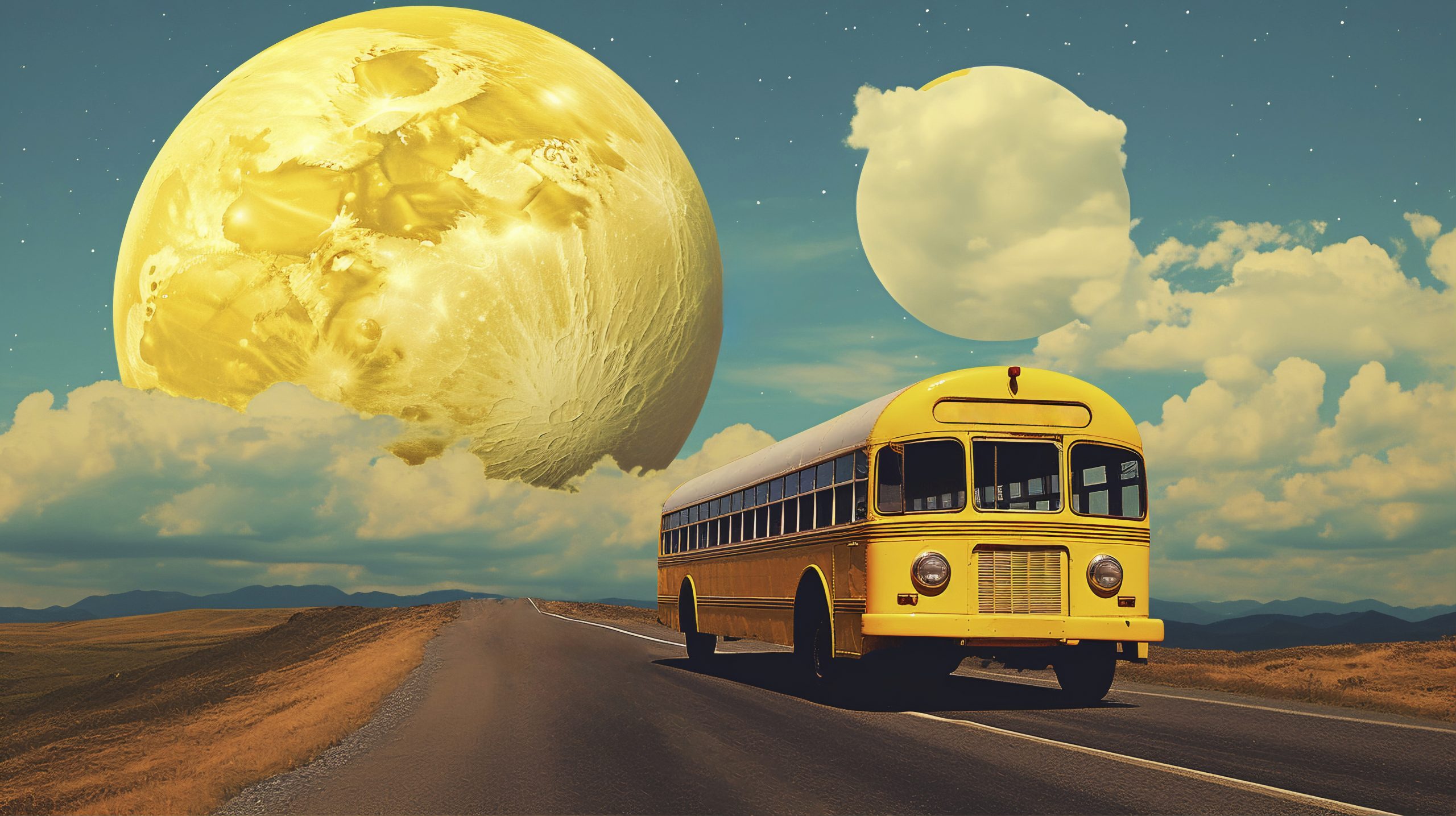
How School Bus Fleet Maintenance Software Reduces Downtime
Do you think downtime in school bus fleets is just a scheduling hiccup? Not at all! It can disrupt daily operations, delay students’ pickups, and cause serious safety and compliance concerns. For small and mid-sized operators, even a single out-of-service bus can impact dozens of students and strain resources. Frequent breakdowns lead to missed routes, emergency repairs, and frustrated parents. This is where school bus fleet maintenance software becomes essential- helping to reduce unexpected failures, automate service schedules, and keep your fleet running on time and within budget.

Understanding the Cost of Downtime in School Bus Fleet Operations
Downtime in school bus operations comes with both visible and hidden costs. When a bus breaks down unexpectedly, it leads to missed routes, last-minute scheduling chaos, and the need for expensive emergency repairs. For small and mid-sized operators, this often means rerouting limited backup vehicles or hiring external transport—both of which drive up costs.
Beyond direct expenses, downtime affects service quality and stakeholder trust. Delays cause student tardiness, upset parents, and can even raise safety concerns if buses break down mid-route. Over time, repeated issues can lead to reputational damage, reduced contract renewals, and strained relationships with schools.
There’s also long-term wear on vehicles when maintenance is reactive instead of preventive. Breakdowns often result from neglecting minor issues that escalate over time—leading to costlier repairs and shorter vehicle lifespans. Downtime is more than an inconvenience—it’s a drain on finances, efficiency, and customer confidence.
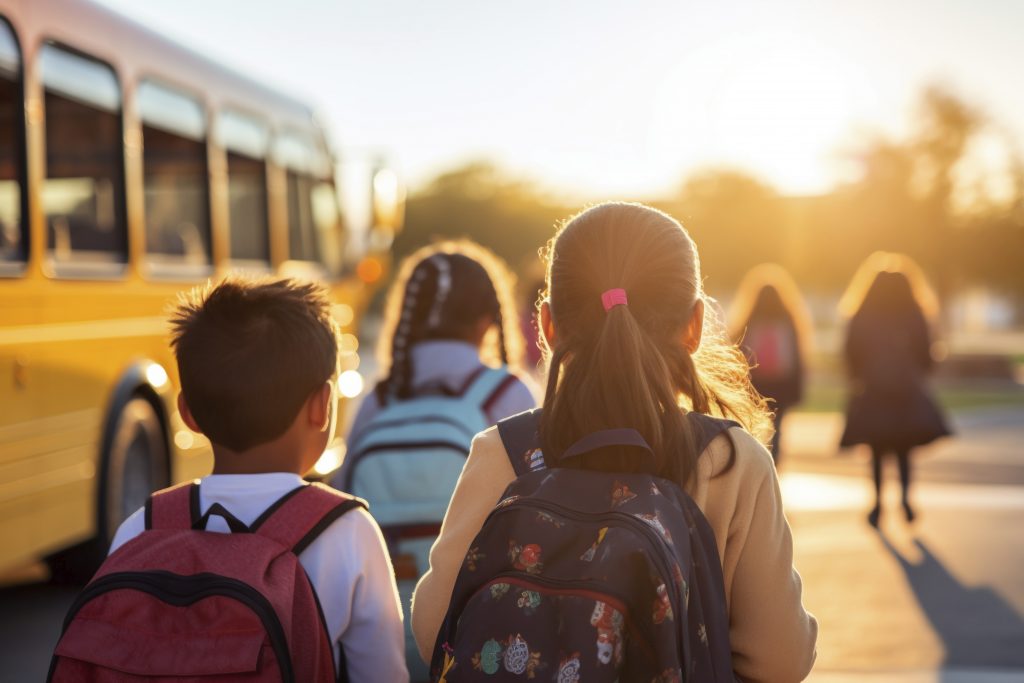
Common Causes of Downtime in School Bus Fleets
Downtime in school bus fleets is often the result of preventable issues that go unnoticed until it’s too late. Let’s take a quick look at the common causes working behind downtime:
One of the most common causes is missed or inconsistent preventive maintenance—oil changes, brake inspections, or tire rotations may be delayed due to manual tracking or lack of reminders, leading to mechanical failures.
Another major contributor is reactive maintenance- waiting for something to break before addressing it. This approach not only increases repair costs but also extends vehicle downtime. Poor communication between drivers, maintenance teams, and fleet managers further delays the resolution of issues that could have been addressed early.
Siloed or inaccessible vehicle data—such as service history, mileage, or inspection reports—makes it harder to identify patterns or plan maintenance proactively. Lastly, unavailable spare parts or delayed approvals from management can stall necessary repairs, keeping buses off the road longer than needed. Together, these factors create costly and disruptive inefficiencies.

What is Fleet Maintenance Software for Schools?
Next-gen school bus fleet maintenance software is a digital tool that helps school transport providers manage the upkeep, servicing, and repair schedules of their vehicles more efficiently.
School bus fleet management software is a digital tool that helps school transport providers manage the upkeep, servicing, and repair schedules of their vehicles more efficiently. Instead of relying on spreadsheets or paper logs, the software automates maintenance tracking, sends service reminders, logs repair history, and monitors vehicle health in real time. It streamlines communication between drivers, mechanics, and fleet managers, ensuring that issues are reported and resolved quickly. Designed to reduce unplanned breakdowns and extend vehicle lifespan, it plays a crucial role in keeping school buses road-ready, safe, and compliant with transport regulations.

How School Bus Fleet Maintenance Software Reduces Downtime
Downtime can cripple day-to-day school transportation operations, especially for small and mid-sized fleets with limited backup options. School bus software tackles this challenge head-on by offering a digital, centralized solution that helps keep buses road-ready and reduces the risk of sudden failures. Here’s how:
1. Automates Preventive Maintenance Scheduling
Preventive maintenance is the cornerstone of fleet reliability, yet it’s often missed due to manual tracking. School bus fleet maintenance software lets you automate service schedules based on mileage, usage hours, or time intervals. It sends real-time reminders to mechanics and managers for essential tasks like oil changes, tire rotations, or brake inspections—helping you avoid breakdowns before they happen. This proactive approach ensures buses are serviced on time, preventing costly emergency repairs and minimizing unexpected downtime that disrupts routes and parent trust.
2. Tracks Real-Time Vehicle Health
With built-in integrations for GPS and telematics systems, school bus fleet management software can monitor vehicle performance in real time. It alerts fleet managers to warning signs—such as engine faults, low battery levels, or overheating—before they escalate into major failures. By diagnosing issues early, you can schedule repairs during off-peak hours instead of reacting to roadside breakdowns. With this real-time visibility, significantly cuts downtime and boosts operational efficiency.
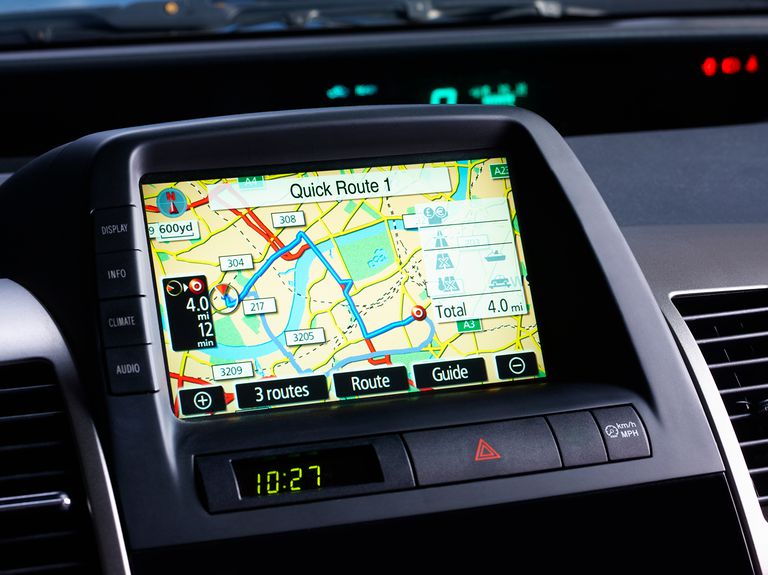
3. Improves Maintenance Workflow Efficiency
The school bus routing software centralizes work orders, repair requests, and maintenance history. Instead of relying on scattered notes or verbal updates, mechanics and fleet managers can collaborate through a shared dashboard. Tasks are digitally assigned, tracked, and closed—ensuring nothing slips through the cracks. You can also generate reports to analyze service timelines and mechanic productivity, which helps identify bottlenecks. Faster turnaround on repairs means buses get back on the road quicker.
4. Enhances Inventory and Parts Management
The unavailability of critical parts often leads to delayed repairs. Maintenance software tracks inventory in real-time, alerts you when supplies are low, and helps reorder parts before you run out. Some systems also link with vendors for faster procurement. A school bus tracking system ensures that needed components are always on hand—reducing wait times and avoiding unnecessary downtime caused by parts shortages.

Small & Mid-Sized School Bus Fleet Managers Need to Act Now
For small and mid-sized school bus operators, every vehicle counts. A single bus out of service can disrupt multiple routes, delay hundreds of students, and create unnecessary stress for staff and parents. Unlike larger fleets with greater flexibility, smaller operations don’t have the luxury of excess capacity—making downtime far more costly and difficult to manage.
Relying on paper logs, manual reminders, or outdated systems to manage maintenance only increases the risk of breakdowns, missed inspections, and compliance issues. As the demands on school transportation grow—tight schedules, safety expectations, and regulatory pressures—operators need smarter tools to stay ahead.
This is where school bus gps tracking system becomes a critical asset. It doesn’t just improve vehicle uptime—it helps you work smarter, prevent expensive repairs, and maintain a reputation for reliability and safety. With automated scheduling, real-time alerts, and streamlined workflows, the software empowers you to take control of your operations rather than constantly reacting to problems.
The longer you wait to digitize maintenance with reliable school bus fleet maintenance software, the more likely you are to face avoidable issues that hurt your bottom line. Now is the time to modernize, minimize risk, and ensure every bus runs when it’s needed most. Downtime isn’t optional—readiness should be.
